Flexible Vacuum Form Plastic Sheets for Any Project
- Akash Pathak
- Aug 23, 2024
- 5 min read
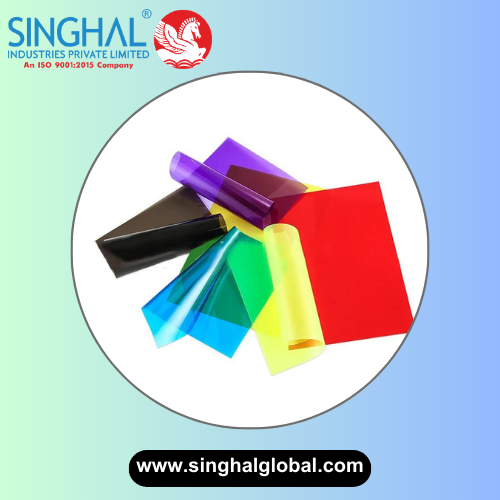
In the realm of manufacturing and prototyping, flexible vacuum form plastic sheets have emerged as indispensable tools, transforming how industries approach product design and development. These sheets, primarily used in the vacuum forming process, offer unparalleled versatility and efficiency. This article delves into the world of flexible vacuum form plastic sheets, exploring their applications, advantages, and considerations, including their pricing and the most frequently asked questions surrounding their use.
Understanding Vacuum Forming and Plastic Sheets
Vacuum forming is a thermoforming process where a plastic sheet is heated until pliable, then draped over a mold. A vacuum is applied to pull the plastic sheet tightly around the mold, creating a detailed, custom shape. This method is favored for its ability to produce complex shapes quickly and cost-effectively, making it ideal for creating prototypes, packaging, and even final products.
Plastic sheets for vacuum forming, particularly flexible ones, are central to this process. These sheets come in various types, each offering unique properties suited to different applications. They are generally made from thermoformable plastics, which become malleable when heated and retain their shape once cooled. Thermoform plastic sheets for vacuum forming are typically composed of materials like ABS (Acrylonitrile Butadiene Styrene), polycarbonate, PETG (Polyethylene Terephthalate Glycol), and PVC (Polyvinyl Chloride), among others.
Applications and Benefits
Flexible vacuum form plastic sheets are used across a wide range of industries due to their adaptability and performance. In the automotive sector, they are employed to create detailed interior panels and dashboard components. The medical field utilizes these sheets for creating custom trays and packaging for medical devices. Retailers use them for point-of-sale displays and packaging. Even in the aerospace industry, these sheets are used for producing lightweight, durable parts.
One of the primary advantages of using flexible vacuum form plastic sheets is their versatility. They can be molded into intricate shapes and designs, allowing for high customization. Additionally, the ability to quickly produce prototypes and low-volume production runs makes them ideal for testing and refining designs before committing to large-scale manufacturing. The flexibility of these sheets also means they can be used in applications requiring varying levels of rigidity, from highly flexible trays to more rigid structural components.
Choosing the Right Plastic Sheets
Choosing the right plastic sheets for vacuum forming is a crucial decision that impacts the quality and durability of the final product. With numerous options available in the market, selecting the ideal material requires careful consideration of factors such as material properties, thickness, and the intended application. Plastic sheets for vacuum forming must be chosen based on their ability to withstand the vacuum forming process, which involves heating the plastic until it becomes pliable and then stretching it over a mold. Different types of thermoform Plastic sheets for vacuum forming, such as ABS, polycarbonate, and PETG, offer varying levels of flexibility, strength, and clarity. For instance, ABS sheets are known for their excellent impact resistance and toughness, making them suitable for parts that require durability. On the other hand, PETG sheets are favored for their clarity and ease of forming, which makes them ideal for creating transparent or visually appealing components. The choice of material will significantly influence the overall performance and longevity of the formed product.
Another critical factor to consider when choosing the right plastic sheets for your project is the thickness of the sheets. The thickness determines not only the rigidity and structural integrity of the final product but also its weight and flexibility. Thicker sheets provide more support and durability, making them ideal for applications that require a high degree of strength, such as automotive parts or protective covers. In contrast, thinner sheets offer greater flexibility and are better suited for projects that require lightweight components, such as packaging or display items. Additionally, the Thermoform plastic sheets for vacuum forming must be compatible with the specific mold design to achieve the desired shape and detail. The vacuum form plastic sheets price can also vary significantly based on the material type, thickness, and sheet size. Understanding these factors can help manufacturers make cost-effective decisions without compromising on the quality of the final product.
In addition to material properties and thickness, the intended use of the product is a vital consideration when selecting plastic sheets for vacuum forming. Different applications require different properties from the plastic sheets. For example, products used in outdoor environments need materials with high UV resistance and weatherability, while products designed for food packaging must comply with safety regulations and be free from toxic chemicals. Evaluating the Vacuum form plastic sheets price relative to their performance characteristics is also essential. While high-quality materials might come with a higher initial cost, they can offer better durability and a longer lifespan, ultimately saving costs in the long run by reducing the need for frequent replacements or repairs. Choosing the right thermoform plastic sheets for vacuum forming involves balancing the material properties, thickness, and cost to meet the specific needs of the project, ensuring the final product is both functional and cost-effective.
Conclusion
Flexible vacuum form plastic sheets are a vital component in modern manufacturing and design, offering flexibility, durability, and customization. Understanding the various types of plastics available, their applications, and their cost implications is crucial for making informed decisions. By selecting the right materials and considering environmental impacts, you can ensure that your projects are not only efficient but also sustainable. Whether for prototyping, packaging, or final product creation, these versatile sheets provide the adaptability needed to bring a wide range of designs to life.
Frequently Asked Questions
What are the main differences between ABS and PETG plastic sheets for vacuum forming?
ABS and PETG are both popular choices for vacuum forming, but they have distinct properties. ABS is known for its high impact resistance and durability, making it suitable for parts that will undergo rough use. It also offers good dimensional stability, which is essential for maintaining the shape of complex forms. PETG, on the other hand, is praised for its clarity and ease of processing. It is less impact-resistant than ABS but offers superior clarity and is easier to thermoform, making it a preferred choice for applications where transparency and ease of processing are crucial.
Can flexible vacuum form plastic sheets be used for outdoor applications?
Yes, some flexible vacuum form plastic sheets are suitable for outdoor use, but their performance will depend on the specific type of plastic and any additional treatments. For outdoor applications, it’s essential to select materials with good UV resistance and weatherability. Polycarbonate and certain types of treated PVC sheets are often used for outdoor applications due to their ability to withstand environmental factors like sunlight, rain, and temperature fluctuations.
How can I determine the right thickness of plastic sheet for my project?
The right thickness of plastic sheet depends on the requirements of your project. Generally, thicker sheets provide more rigidity and durability, while thinner sheets offer greater flexibility. For applications requiring strength and structural integrity, such as automotive parts or protective covers, thicker sheets are preferred. For more flexible uses, like custom trays or packaging, thinner sheets may be sufficient. It's also important to consider the size of the mold and the complexity of the design when selecting sheet thickness.
Comments